Sustainability and the Concrete Supply Chain
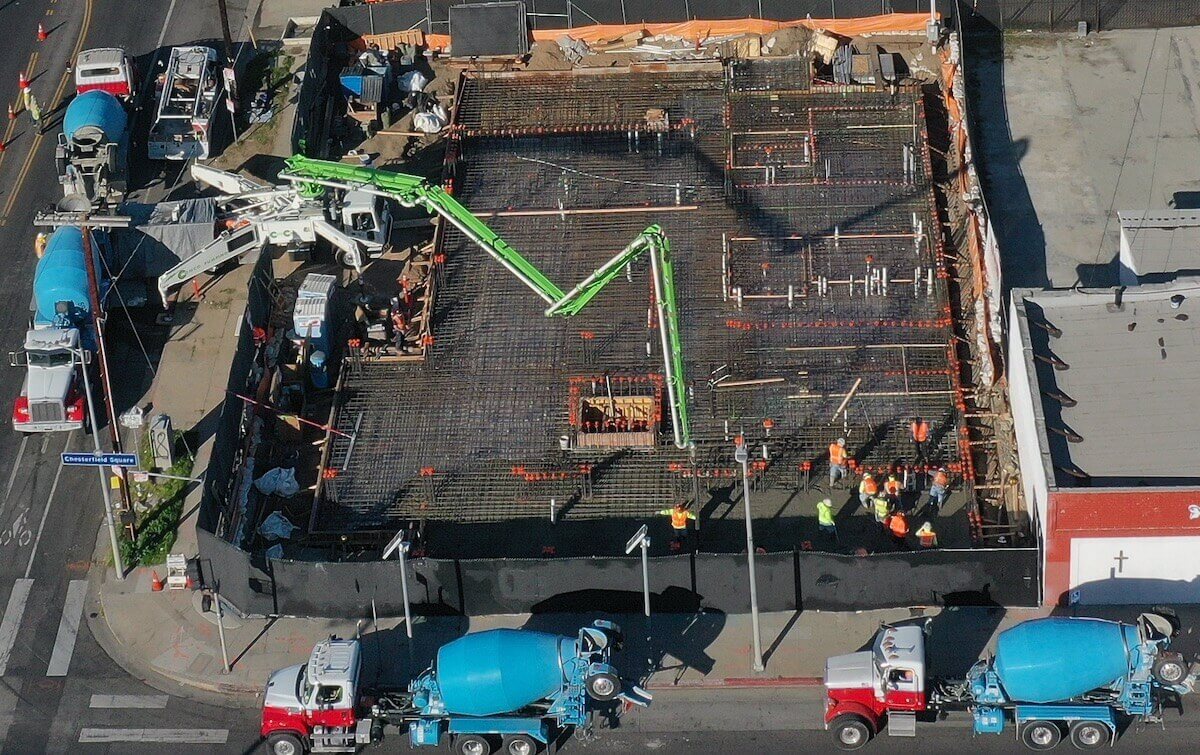
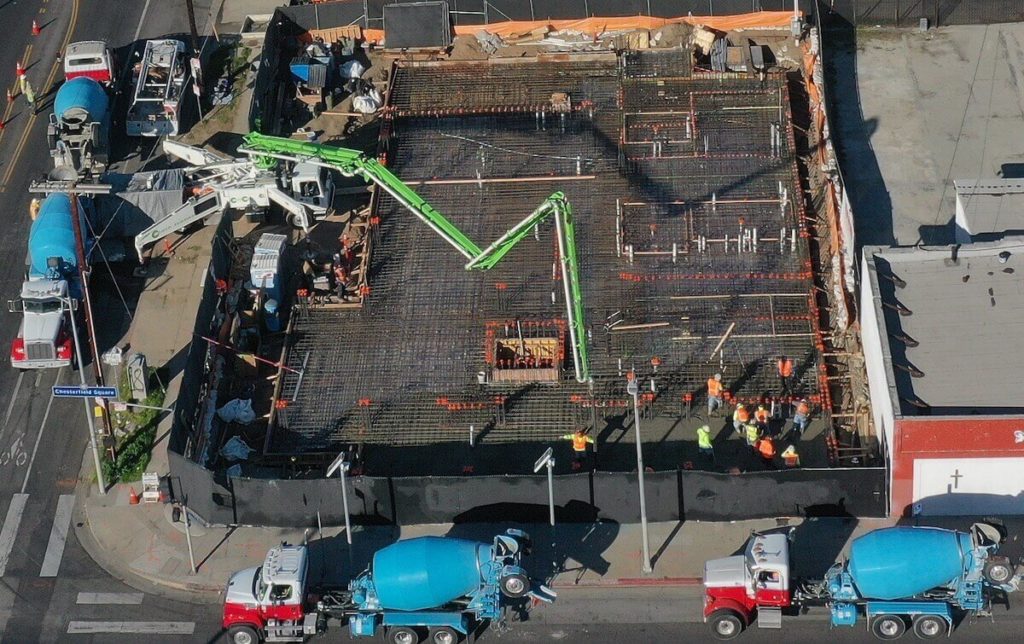
Only 25 years ago, the raw materials necessary to produce ready-mix concrete — namely, cement, fly ash, and aggregates — were far more available than they are now. These materials were not only plentiful, but they were produced near the markets they serviced. The cement and aggregates industry employed many individuals with local, well-paying union jobs; in turn, local businesses benefited from the commerce these companies generated. As an industry, we used these resources as if there were an infinite supply. Need to strengthen your concrete? Just add another sack of cement. Need the concrete to set a little faster? Just add more cement to the mix.
But in the years since, many cement plants, such as Davenport, Colton, Oswego, Crestmore, and Cupertino, have shut off their kilns and ceased production. The same is true of aggregate pits such as Steilacoom, Radum, Felton, Olympia, and Maury Island. And the fly ash that came from Centralia, WA is no longer available.
These sources of raw materials are no longer at our disposal, yet very little domestic production has been brought online to replace them. In the states where Conco primarily does business (California, Washington, and Oregon), no greenfield cement manufacturing plants have been built since the 1960s. The aggregate industry is not faring much better. A company must invest up to 10 years in applying for a permit to harvest new reserves, with no guarantee that it will actually obtain one, let alone successfully extract aggregate. Moreover, due to environmental and process changes, very little fly ash can be distributed economically out of west coast terminals.
Imports have filled the void between supply and demand, and our supply chain for raw materials now stretches halfway around the world. Cement production is now supplemented from China, Vietnam, and Mexico, among other places. Slag is imported from China and Japan. There have been attempts to bring fly ash from India, and aggregates are coming down the coast from British Columbia.
The logistical challenges facing the industry today are exponentially more daunting than they were in the past. Raw materials such as cement and slag cannot be shipped economically to a port unless the terminal has both deep water access and sufficient storage capacity so that the cargo can be unloaded quickly and efficiently. However, there are only a limited number of port sites capable of handling large ships, and many of those can only hold shipments for about two weeks to one month.
Given the limited availability of suitable ports, an importer arranging a cement shipment from Asia must walk a fine line. On the one hand, the importer must factor a lead time of at least 90 days into its schedule because the trip across the Pacific alone takes nearly one month, and it must accurately project that there will be sufficient storage available to unload the ship. On the other hand, the importer must avoid waiting too long to procure the cement; otherwise, there’s a risk that the supplier may run out of cement.
The supply chain can be affected by any number of unexpected circumstances. What happens when it rains for a week straight, curtailing demand for concrete? What if a competitor runs out of cement and their customers suddenly shift to your facility, causing shipments to increase dramatically? How does a tsunami over the South China Sea impact deliveries? How does a kiln outage in Vietnam impact the availability of cement in California? Such incidents will impact the supply chain, causing oversupply (and the added expense of demurrage for ships) and/or the potential for shortages in the local marketplace. As the supply chain for raw materials lengthens, the frequency of over-supply and under-supply issues will escalate.
As an industry, we must assume that the raw materials we need will become increasingly expensive and, in some cases, harder to obtain. Furthermore, with the spotlight being placed on the carbon-intensive process involved in manufacturing cement, it is in the industry’s best interest to understand the changing landscape and to work towards solutions that reduce our carbon footprint without compromising the structural integrity of the structures we build.
Specifications often include requirements that have the potential to unnecessarily increase the carbon footprint of the concrete. Here are some common examples:
- A requirement that the same source of cement be used throughout the project. If cement is sourced from halfway around the world, there is an increased potential that there may be times when that cement is not available. This should only be required on architectural finished concrete such as colored sitework.
- A minimum cement content requirement that accompanies a PSI requirement. If the ready-mix producer is able to meet the PSI requirement in a mix design (with the proper safety factor) using less cement than is mandated by the minimum cement requirement, why not let him do so?
- A maximum amount of supplementary cementitious material. Why not let a ready-mix producer use less cement and more green products like fly ash or slag if the rest of the design criteria are met?
- A required water/cement ratio in the mix design that conflicts with strength requirements. Specifications often dictate a water/cement ratio that is much lower than is necessary to meet the design strength. This leads to the use of more cement than is required to meet strengths.
- A requirement based on outdated cement specifications. The cement industry has worked to lower its carbon footprint through changes to the processes and products it offers. One of the newer formulations is an ASTM C595 Type 1L cement that inter-grinds limestone into the cement, reducing the CO2 footprint by approximately 10% versus the typical ASTM C150 Type II/V cement, with no discernible loss in performance.
- A requirement that all mixes to be designed using 28-day break criteria. When using supplemental cementitious materials, these mixes tend to be slower in gaining early strengths, but ultimately achieve equal or higher strengths. If the structure is not being fully loaded where this early strength criteria is needed, savings can be made by pushing out strength requirements for 56 days or more.
In light of such developments, we must revisit the usefulness of the requirements included in concerete specifications.
Below are results from a study conducted by Central Concrete comparing 3,000, 5,000 and 7,000 PSI mixes designed with some of the requirements listed above. Mix designs were formulated using no supplementary cementitious materials (SCM’s) and 70% SCM’s to achieve the same strength performance. In the study, the Global Warming Potential (GWP) of the various mix designs were compared. GWP values were derived from the product-specific Environmental Product Declaration (EPD) associated with the raw materials used to construct the mix designs.
Specification Requirement | 3,000 psi | 5,000 psi | 7,000 psi | |||
No SCM | 70% SCM | No SCM | 70% SCM | No SCM | 70% SCM | |
0.45 w/cm Maximum | 335 | 174 | 335 | 175 | 409 | 227 |
Minimum 6 sack Content (564 lb/cy) | 330 | 192 | 330 | |||
Performance at 28 Days | 277 | 160 | 296 | 187 | 376 | |
Performance at 56 Days | 220 | 142 | 281 | 185 | 326 | 200 |
Table 1 – GWP Values (kg CO2eq/m3) from Product-Specific EPDs at One Central Concrete Plant
The plot below summarizes the values from Table 1. This shows the range of GWP values from high (mix without SCMs) to low (mix with maximum SCM content). Specific selection of a mix design in that range will vary depending on the contractor’s requirements for schedule, placement method, finishing requirements, ambient conditions, etc.
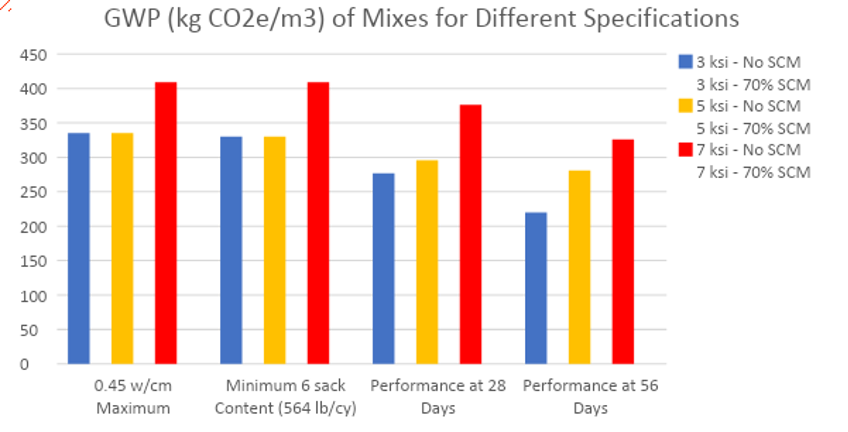
Another way to look at the data from the table is with the two plots below. They demonstrate that the mixes with maximum SCM content have much lower GWP values, particularly at higher strengths, and are less impacted by prescriptive requirements.
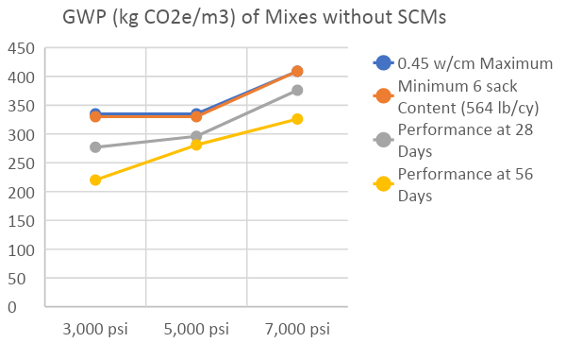
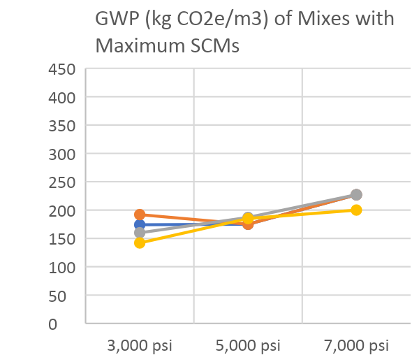
The study shows that the GWP of the mix designs can be reduced significantly by using SCM’s and eliminating prescriptive requirements such as maintaining a certain water/cement ratio, using a minimum quantity of cement in the mix, or mandating that a concrete mix meet designed strength within 28 days. History has proven that the GWP of a concrete mix can be reduced in half.
As a concrete contractor that has placed millions of cubic yards of concrete over the years, Conco has seen marked differences in concrete specifications as they relate to sustainability and performance. With our knowledge of local materials and vast experience in pumping, placing, and finishing concrete, we welcome the opportunity to review proposed concrete specifications and recommend alternatives that will achieve sustainability goals without compromising structural integrity. Let us work with you to find concrete solutions.